Plastics Compounder Maximizes Production Agility With Modular Conveyor System
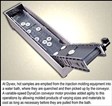
"Truly modular" conveyor system enhances Dyvex Industries' manufacturing and customer services, adapting promptly to changing production, scheduling and manpower requirements.
Mention the term "agile" in business these days and some people will think you're talking about software, or some other esoteric usage. But in a manufacturing context, agility has decidedly physical attributes: the ability to move quickly, nimbly, and with dexterity - qualities that are always a good idea on the production floor.
Dyvex Industries® thinks about agility in every sense of the word. It permeates the business, providing a unique positioning and real competitive advantages in an industry where products and services are often regarded as generic as table salt. Agility gives Dyvex the means to set up and reconfigure its production lines quickly, responding to changing customer needs and promoting customization of orders.
Located in Carbondale, PA, Dyvex is a specialist in compounding technologies, particularly in the creation of customized, highly-loaded additive concentrates in a variety of polymer bases. Dyvex also compounds custom fragrance concentrates for use in scenting polymers, whether to overcome a malodorous plastic compound, add a special fragrance to a plastic product, or produce an aromatic product such as an air freshener.
"We've incorporated agility into our business strategy," says David Pettinato, Dyvex Vice President of Sales and Marketing. "We offer our customers specialized, flexible and highly responsive services, including R&D, injection molded samples, in-house cryogenic grinding services and custom packaging. We even handle orders and drop-ship on behalf of our customers." The name "Dyvex" is derived from "diversified services."
One of the keys to maximizing Dyvex production agility is a DynaCon® variable-speed, modular conveyor system from Dynamic Conveyor Corporation, Muskegon, MI. Constructed of high-impact plastic, the DynaCon system is perfect for Dyvex's light- and medium-duty conveyor applications from R&D operations through packaging.
Composed of lightweight, interlocking modules, a single DynaCon conveyor system meets the needs of a variety of applications throughout the plant, providing Dyvex with the ability to relocate the conveyor and reconfigure it quickly according to their needs.
"We can reconfigure the system in a matter of minutes, add or remove conveyor modules and roll the system from one end of the plant to the other without interrupting work flow," Pettinato explains. "It would be fair to say that the DynaCon system harmonizes with our flexible production operations and our need to quickly meet constantly changing customer requirements."
The benefits of a modular and portable conveyor system were initially recognized in the Dyvex R&D department, where the firm compounds various plastic flakes, pellets and powders to meet specific customer requirements. In order to ensure customer satisfaction and quality control, Dyvex produces injection-molded samples of plastics that will later undergo that process at customer facilities. Hot samples are emptied from the injection molding equipment into a water bath, where they are quenched and then picked up by the conveyor. A variable-speed DynaCon conveyor motor provides added agility to this operations by allowing molded products of varying sizes and materials to cool as long as necessary before they are pulled from the bath.
"We also produce samples of fragrances in plastic chip form, to enable customers to test different scents in the polymer of choice," Pettinato explains. "On occasion, we produce relatively short runs of injection-molded products for customers who want to test market them before tooling up their own facilities, or simply need a limited quantity."
Dyvex also uses the same DynaCon conveyor to transfer materials to its cryogenic grinding equipment, which is a critical in-house operation. "Most compounders send their materials to an outside service for cryogenic grinding," says Pettinato. "We perform this operation in-house to avoid contamination of our customers' materials with particles of some other customer's materials, which can happen at outside grinding services. For example, I might be grinding a polypropylene using critical grades of different resins. Any foreign material left in the grinder could very well corrupt an amount of our customer's material, which could in turn taint a very heat-sensitive application such as a coating.
"We can quickly configure our DynaCon system to convey low-density material to the cryogenic system hopper that would be difficult to carry by auger, due to compaction problems, or by air, since the material would blow all over the place," Pettinato says. "After that operation is completed, the conveyor will most likely be sent on to another job in another department."
The portability, quick reconfiguration and variable speed control of the DynaCon conveyor system also makes it ideal for use in the Dyvex Omnipak International packaging operation, which is a separate company division, although located in the same plant as the compounding operations.
"Our packaging division is a very important service to a wide range of customers," Pettinato says. "This is another area where agility is important. We offer blister-pack packaging of plastic products, plus bulk packaging and even display packaging. We drop-ship to our customers' distribution points and also handle orders directly on behalf of customers. In some cases, the customer never even sees the product. The portability and ease of reconfiguration of the conveyor come into play with this service all the time. We simply roll the conveyor from the production floor, if necessary, and reconfigure it in probably less than half an hour. We can adjust the conveyor to make it more ergonomic for our packaging people, and control the conveyor's speed to adjust for packaging complexities or for the number of people who might be working on that line at the time."
The DynaCon conveyor product line, developed specifically for light- and medium-duty applications, is a totally integrated design that encompasses the entire conveyor system, including a wide choice of interlocking modules and a choice of brushless motors that are suited for even clean-room operations. A number of DynaCon system accessories are available: a feed shield to prevent parts from deflecting off the conveyor, exit chute, and drop-zone reinforcement module. Available electrical accessories include box filling via counting machine cycles, electronic eye for parts counting and placement, as well as electrical controls for indexing, reversing and cutting conveyor power.
For more information on the "Truly Modular" DynaCon conveyor solutions, contact Dynamic Conveyor Corporation, 5980 Grand Haven Road, Muskegon, MI 49441; phone (866) 249-2641; fax (231) 798-7739; or visit the web site www.dynamicconveyor.com.