When The Implant Needs To Last A Lifetime, New Fastener Thread Form Technology Is Key
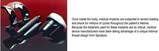
By Del Williams
A unique internal thread form is helping medical device manufacturers combat vibration, shock, and thread loosening for needed safety and performance
With the lives of patients as well as the reputations of surgeons and medical device companies at stake, medical implants face some of the most rigorous performance requirements of any industry. Yet despite all the recent technology applied to implants, they still require simple fasteners to function properly. Once inside the body, these fasteners with their accompanying thread forms often must endure severe loading and shock for millions of cycles throughout the patient's lifetime.

Because these fasteners are so critical, medical device manufacturers have been taking advantage of a unique internal thread design that not only combats vibration and shock but also safeguards product quality and performance whether the implant is permanent or temporary.
The Limitations of Traditional Threaded Fasteners
Traditional threaded fasteners suffer severe limitations wherever shock, vibration, or sustained loading exist. This problem exists due to the female 60° "vee" threads that are prevalent in most fastening systems, which were originally designed to accommodate a variety of unavoidable problems such as drill, tap, and die wear; hole size variation; and errors in placement, machine setup, thread finish, etc. While this design is acceptable for non-critical fastening applications, it is susceptible to self-loosening rotational movement - not something that can be risked with implants in the human body.
Furthermore, common stripping or shearing problems can occur when conventional 60° threads position most of the clamp load on the first engaged thread, permitting subsequent male threads to virtually "float" within the female threads. Testing has found that the first two threads carry as much as 80% of the load, which can be enough to cause shearing or stripping.
Solving Fastening Problems with a New Thread Design
Through the physics of the thread itself, Madison Heights, Mich.-based Spiralock Corp. is offering an alternative thread form designed to address the fastener loosening and stripping problem. The secret to Spiralock's thread form is a 30º "wedge" ramp cut at the root of the female thread. Under clamp load, the crests of the threads on any standard bolt are drawn tightly against the wedge ramp.
The 30º wedge ramp design not only eliminates sideways motion that causes loosening under vibration but also distributes the threaded joint's load throughout all engaged threads. Research studies at both the Massachusetts Institute of Technology and the University of Michigan confirm that the load percentage carried by each engaged thread using a Spiralock tap is much more uniform than with conventional 60° thread forms. Other studies demonstrate that the load percentage on the first engaged thread using a Spiralock tap are also significantly lower, which further reduces the possibility of bolt failure and improves product performance.
Medical Quality Fastening: 1 Million Cycles a Year, Shear Loads to 2,700 Lbs.
Recently, Warsaw, Indiana-based Biomet, Inc. developed an artificial knee implant which closely fits the individual patient's anatomy, creating a wide range of motion and superior joint functioning compared to previously available implants.
Splitting the tibial component of the implant into two pieces fastened with a single screw makes possible the ability to build the knee in a modular fashion so that each component's size can be selected by the surgeon based on the patient's specific anatomy. But, this innovative development is highly dependent on the threaded fastener that must guarantee repetitive loading without loosening.
Knee implant surgery is designed to be permanent, so the implant assembly must function for the rest of the patient's life, without failure. Re-tightening the implant in a second or third operation is not an option. Studies have shown that the human knee is subject to 1,000,000 or more loading cycles per year. Conventional fastening methods such as add-on locking components, adhesives, patches, and inserts will be rejected by the body, and aren't acceptable methods for implant use.
The final choice came down to a snap-fit type locking fastener and the Spiralock thread form. Extensive fatigue tests showed that the snap-fit fasteners tended to work loose under extensive loading, while Spiralock did not fail, regardless of the length and severity of the tests.
The modular tibial system consists of: a titanium alloy tray with fins to resist rotational forces, a polyethylene bearing, and a titanium modular tibial stem which attaches to the tibial tray for improved stability. A standard titanium screw attaches to a Spiralock-tapped hole in the stem to integrate the tray, polyethylene bearing and stem into a single unit using a Morse taper fit between the tray and stem.
After several years of in body application, not a single screw fastened with the Spiralock thread form has come loose.
Though many implants are designed for permanent function without revision, some in fact ultimately require revision due to unavoidable wear over time or the temporary nature of the implant itself. In these cases, the implant must nevertheless function flawlessly while inside the patient, while keeping the healing, revision, or removal process as simple as possible.
A recent Biomet elbow replacement device, for example, joins a polyethylene bearing of an ulna component with two cobalt chrome articulating surfaces on the humeral component using the Spiralock thread.
"We had to find a way to lock the articulation together in a compact form without violating the elbow condyles," said Matt Brzozowski, a Biomet Extremities Product Manager. "To replicate anatomy as closely as possible, we not only had to keep the threads secure, but also wanted to provide a simpler approach to the articulating components should additional surgery be necessary."
C-clips, specialized retaining rings, and other fasteners proved too cumbersome and costly for the design. For vibration control, loading, and shear strength, Spiralock threads were chosen in conjunction with titanium screws. The titanium screws survived a shear test to approximately 2,700 lbs., at which point the screws broke but remained locked in the thread form.
Besides vibration resistance and trustworthy thread locking, the Spiralock thread also can provide anatomic and surgical benefits.
"The threads helped us match each patient specifically," says Brzozowski. "Because the bearing is consistent with respect to the screw, we're able to match any humeral sized component with any ulna sized component. For example, if a patient has a distal fracture or distal stress riser in the humerus and needs total elbow replacement, we can combine a small ulna component with a long humeral component to get past the fracture for more stability."
"Moreover, the way the threads work allows the surgeon to access them from the posterior side of the elbow," continues Brzozowski. "That way, if revision surgery is necessary, the humeral stem may remain in place and surgeons don't have to take the component out. For patients, that means less time in the operating room."
The Spiralock thread also helped medical device manufacturer Boston Endo-Surgical Technologies, Inc., based in Hampton, New Hampshire, improve an innovative internal limb-lengthening device, currently used to lengthen the femur or tibia in cases where bone has stopped growing or has been shattered. Prior to the development of the internal limb-lengthening device, up to eight external pins had to penetrate from the skin to the femur or tibia in order to attach an external device, with a likely possibility of infection.
An unusual left-hand Spiralock thread now firmly joins the limb-lengthener's lead screw with a redesigned nut-screw, and with appropriate torque applied, the screw joint will not loosen. When surgically placed in a patient's femur or tibia, the appropriate bone can now be lengthened up to eighty millimeters while the patient remains mobile.
Spiralock makes threads as small as #0-80 (80 threads per inch) as well as double lead threads, which spin on twice as fast with every rotation to decrease time in surgery.
For more info on Spiralock Corp. technology and products, visit www.spiralock.com; email slinfo@spiralock.com; call (800) 521-2688; fax (248) 543-1403; or write to them at Madison Tech Center, PO Box 71629, Madison Heights, MI 48071.